Links und rechts in der gewaltigen Werkshalle stehen die Fräsen und Roboter in geraden Reihen, in der Luft liegt ein Rütteln und Brummen. Peter Koevago grüßt mit einem Nicken die Kollegen. „Da hinten ist mein Arbeitsplatz“, sagt er und zeigt auf eine Maschine, an der ein Roboterarm hinter Glasscheiben kleine Edelstahlrohlinge schleift. Es sind Bauteile für Dieselpumpen, und Peter Koevago steuert die Arbeit mithilfe eines Touchscreens.
Die Arbeit der Zukunft
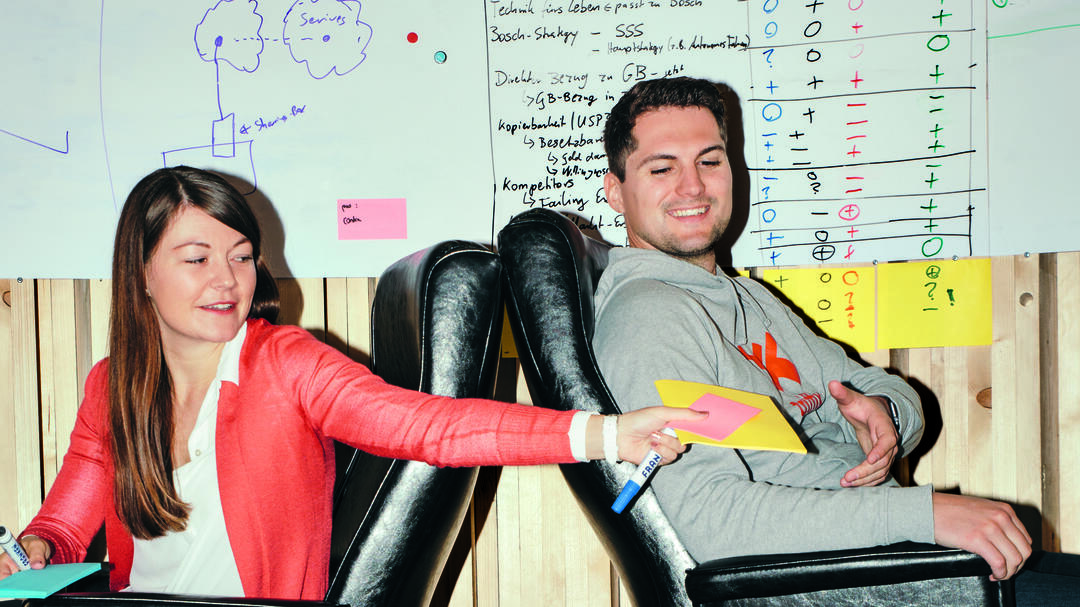
„Als Industriemeister ist es doch logisch, dass ich mich für alles Neue interessiere. “
Heute reiht sich hier ein Roboter an den anderen. Aber auch Koevago ist nicht mehr der Geselle, der er damals war: An der Abendschule bildete er sich zum Industriemeister Metall weiter, und zurzeit schließt er seine nächste Weiterbildung ab: „Fachkraft Industrie 4.0“ heißt das Zertifikat, ihm fehlt nur noch die Abschlussprüfung. Im Kurs geht es um technologische Inhalte genauso wie um Arbeitsmethoden: Welche Technologien gibt es? Wie werden Daten übertragen? Wie funktionieren Logistik und Supply Chains in einer digitalen Welt? „Ich bin Industriemeister“, sagt Koevago: „Da ist es doch logisch, dass ich mich für alles Neue interessiere.“
Sein Arbeitsplatz ist weitgehend automatisiert. Wenn das Ausgangsmaterial auszugehen droht, ordert der Computer automatisch Nachschub. An einem großen Bildschirm, mitten in der Produktionshalle, laufen alle Daten zusammen: Wie gut die Fertigung läuft, wie der Auftragseingang aussieht, welche Parameter die Produkte haben müssen, wo es Schwierigkeiten gibt. Zu Schichtbeginn treffen sich hier die Mitarbeiter zu einer Besprechung. „Früher hatten wir dafür endlos viele Tafeln, wo wir die Daten per Hand eingetragen haben“, sagt Koevago. Und vor allem: In einem Schwesterwerk in Tschechien laufen die gleichen Produkte vom Band wie hier in Stuttgart-Feuerbach. Wenn eine Maschine eine Störung hat, erfahren die Mitarbeiter sofort, ob ihre Kollegen im anderen Werk schon einmal ein ähnliches Problem hatten – und wie sie es lösen konnten. Peter Koevagos Werdegang zeigt exemplarisch drei wichtige Merkmale des derzeitigen Wandels. Erstens: Die Arbeitswelt verändert sich so rapide, dass selbst Leute im mittleren Alter in ihrer Laufbahn schon grundlegend umdenken und umlernen müssen. Zweitens: Die Schlagzahl tief greifender Veränderungen nimmt immer weiter zu. Und drittens: Ändern müssen sich die Unternehmen mit ihren Mitarbeitern zusammen. Die Ausbildung zum Experten für die Industrie 4.0 zum Beispiel, die Peter Koevago gerade durchläuft, hat Bosch mit der Industrie- und Handelskammer zusammen konzipiert.
Lebenslanges Lernen im Unternehmen
Aber der Begriff Weiterbildung bezeichnet längst nicht mehr nur die traditionellen Fortbildungen, zu denen sich die Mitarbeiter mit einem Kursleiter in einen Seminarraum zurückziehen. Das Lernen ist bei vielen Unternehmen inzwischen fest im Alltag verankert; manche krempeln sogar ihre gesamte Organisationsstruktur um, damit die Mitarbeiter voneinander lernen können – quasi nebenbei, während sie ihre Arbeit erledigen.
„Ich bin hier in eine ganz neue Welt eingetaucht“, sagt Lisa Zeller, ihre Augen leuchten. Sie sitzt in einem Konferenzraum, den ein Künstler aus groben Holzbohlen gezimmert hat. Er steht inmitten der 5.000-Quadratmeter-Halle, in der einige Dutzend Leute an ihren Schreibtischen arbeiten, die meisten von ihnen in den Dreißigern. „Hier sitzt ein Start-up neben dem anderen“, erklärt Lisa Zeller und zeigt auf riesige Pinnwände entlang der Betonwand. Vor ein paar Monaten war sie noch Marketingexpertin bei Bosch, genau genommen hat sie den Konzern auch nicht verlassen. Denn alle Start-ups in dieser alten Fabrikhalle sind Tochterfirmen von Bosch – nur eben losgelöst von den Hierarchien und Strukturen, die es in dem Konzern mit seinen weltweit mehr als 400.000 Mitarbeitern nun einmal gibt. „Ich habe schon ein paar Wochen gebraucht, bis ich mich an das Fehlen von festen Strukturen gewöhnt habe“, sagt Lisa Zeller.
Alle Angestellten von Bosch können sich um die Mitarbeit in einem der sogenannten Discovery Teams bewerben. Ein paar Wochen lang sitzen die ausgewählten Kandidaten dann mit Kollegen zusammen, die sich noch nie zuvor gesehen haben – und entwickeln gemeinsam Ideen für ein neues Geschäftsmodell. Wenn sie am Schluss die Jury überzeugen, erhalten sie nicht nur das Startkapital, sondern können auch in Vollzeit an ihrer Idee arbeiten.
Für Bosch dürfte das Konzept aufgehen. Entweder die Geschäftsmodelle von triffix und den anderen firmeneigenen Start-ups setzen sich durch, dann sind sie womöglich eine Goldgrube. Oder sie scheitern – dann können die Mitarbeiter wieder in den Konzern zurückkehren, und zwar mit all dem Wissen und den Erfahrungen, die sie in ihrer Zeit im Start-up gewonnen haben. Und die Einblicke nehmen jeden Tag zu, betont Florian Hachenberger: „Sie glauben gar nicht, wie viele Reisegruppen bei uns durch die Büros kommen!“ Bosch-Mitarbeiter sind es vor allem, die bei triffix neugierig hereinschauen und wissen wollen, was hier in der alten Werkshalle heute so entsteht. Man setzt sich zusammen und plaudert. Lisa Zeller hat dabei einen erfahrenen Vertriebsprofi kennengelernt, mit dem sie sich ab und zu trifft, um von ihm neue Kniffe zu lernen – sie ist beim Start-up für den Vertrieb zuständig und muss sich das Feld erst selbst erarbeiten. Oder, anderes Beispiel: „Neulich war eine Gruppe von früheren Führungskräften hier bei uns, die jetzt in Rente sind. Wir saßen stundenlang zusammen und haben Erfahrungen ausgetauscht“, sagt Hachenberger.
Wie Unternehmen die neue Arbeit gestalten
Die alten Hasen und die jungen Start-up-Gründer – auch so kann Weiterbildung aussehen. „Die Digitalisierung ist zunächst eine rein technische Entwicklung“, sagt Steffen Fischer, der beim Bundesverband der Personalmanager die Fachgruppe zum strategischen Personalmanagement leitet. „Für Unternehmen liegt die Herausforderung darin, diese Entwicklung mit den sozialen Aspekten zu verbinden.“ Mit diesem Spagat beschäftigen sich derzeit fast alle Firmen: Einerseits wird die Produktion immer stärker automatisiert, werden von der Entwicklung bis zur Logistik alle denkbaren Bereiche miteinander vernetzt. Andererseits drohen viele Mitarbeiter aus allen Hierarchieebenen angesichts der schnellen Veränderungen auf der Strecke zu bleiben. „Es geht dabei zum Beispiel um die Gestaltung von Arbeitsort und Arbeitszeit, darum, wie viel tatsächliche Freiheit jeder Mitarbeiter für seinen eigenen Verantwortungsbereich bekommt und wie man die Personalführung modern gestaltet.“ Unter Personalchefs werden diese Fragen unter dem abstrakten Schlagwort new work zusammengefasst, und wenn Experten wie Steffen Fischer darüber sprechen, schwingt als Leitmotiv immer die Überlegung mit, wie sich Unternehmen und vor allem die Mitarbeiter darauf vorbereiten lassen.
„Wir reden hier von einem Kulturwandel“, sagt Steffen Fischer, „und der lässt sich nicht einfach mit Fortbildungen bewältigen, wie sie in der Vergangenheit üblich waren.“ Nötig seien tief greifende Änderungen nicht nur beim Lernen, sondern auch beim Arbeiten: Früher etwa traf man sich im Konferenzraum und fällte dort die Entscheidungen. Heute gibt es in Büroetagen überall gemütliche Ecken mit Stehtischen und Kaffeemaschinen. „Wer noch in der alten Kultur aufgewachsen ist, wundert sich darüber“, sagt Steffen Fischer. Aber diese Einrichtungen seien natürlich weder Selbstzweck noch Ausdruck eines Zeitgeistes. „Der informelle Austausch ist tatsächlich äußerst effektiv.“ Dieses scheinbar banale Beispiel stehe für die Neuerungen, die in der Arbeitswelt auch weit unter der Oberfläche stattfänden.
Austausch als Kern der Weiterbildung
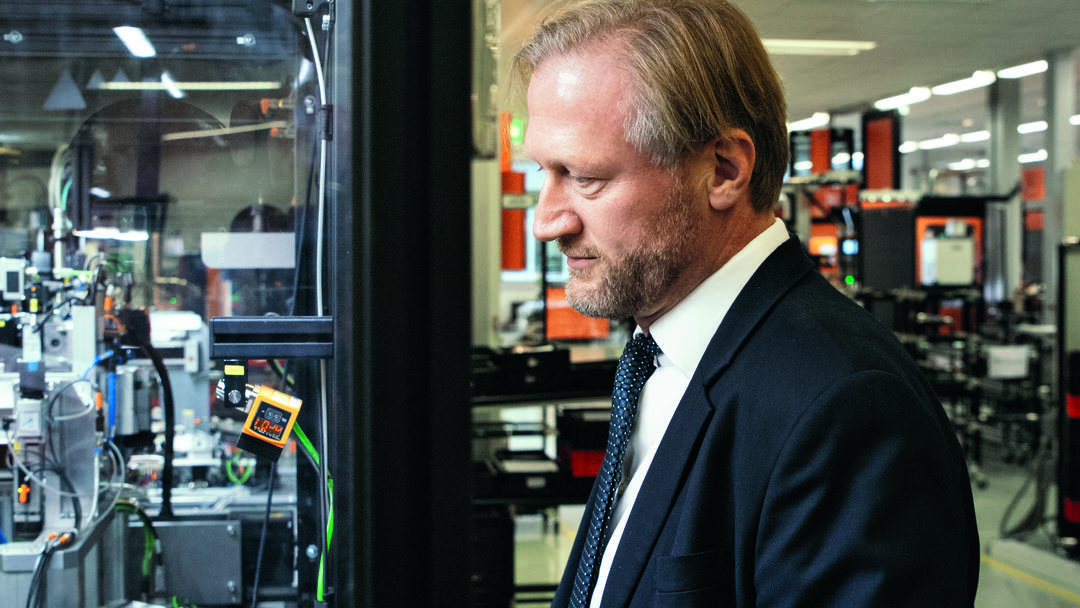
„Manchmal sind 50 Kollegen beteiligt, um gemeinsam etwas Neues zu entwickeln. “
Steffen Fischer erlebt die Veränderungen hautnah mit. Denn neben seiner ehrenamtlichen Funktion beim Bundesverband der Personalmanager ist er auch Personalchef und Mitglied der zentralen Geschäftsführung bei der Firma ifm. Das Elektronik-Unternehmen, das seinen Sitz in Essen und seinen Hauptentwicklungs- und Produktionsstandort in Tettnang am Bodensee hat, kennt außerhalb von Fachkreisen kaum jemand. Mit seinen 7.000 Mitarbeitern und einem Jahresumsatz von zuletzt fast einer Milliarde Euro gehört der Hersteller von Hightech-Sensoren zu den Hidden Champions.
Regelmäßig treffen sich die in aller Welt stationierten Mitarbeiter zum Austausch per Video. Gestern erst hat ein Team aus der Produktentwicklung über die neuesten Entwicklungen berichtet. „Auch Kollegen, die nicht unmittelbar vom Fach sind, sollen mitbekommen, was gerade die aktuellen Themen sind“, sagt Steffen Fischer. Damit dieser Austausch möglich ist, hat er die ifm Lernfabrik ins Leben gerufen – das ist der Oberbegriff für ein sehr weitgefasstes Fortbildungs- und Kommunikationsangebot. Vorträge wie dieser gehören dazu, aber auch Softwaretrainings, Sprachkurse und Seminare für Führungskräfte. Die Besonderheit dabei: Viele der Angebote stammen nicht von externen Trainern, sondern von Fachleuten aus dem Unternehmen, die ihre Kollegen auf dem kurzen Dienstweg schulen. Das solle nicht in erster Linie Kosten sparen, betont Fischer, sondern schlicht abbilden, was im Alltag ohnehin immer stärker passiere – dass sich die vorher getrennten Abteilungen immer besser miteinander vernetzen. „Die arbeitsteiligen Aufgabenzuschnitte, wie es sie in der Vergangenheit gab, funktionieren heute so nicht mehr“, sagt Steffen Fischer. Wurde früher ein neuer Sensor entwickelt, passierte das wasserfallartig: Die Führungskräfte gaben einen Entwicklungsauftrag, der dann nach und nach alle nötigen Abteilungen durchlief, bis schließlich ein Produkt herauskam. „Heute sind manchmal 50 Kollegen aus den verschiedenen Abteilungen beteiligt, um gemeinsam etwas Neues zu entwickeln“, sagt Fischer. Agile Entwicklung heißt dieser Trend, den es auch bei anderen Firmen gibt. Das neue Verfahren sei effizienter und schneller, aber erfordere andere Kompetenzen von jedem Beteiligten: „Und genau dieses Aufeinander-Zugehen, diesen Austausch bilden wir in unseren Weiterbildungsprogrammen ab.“
Mehr Informatiker, Facharbeiter und Ingenieure
Oliver Bucher muss tief hinabsteigen in die Katakomben eines ifm-Werks, um zu zeigen, wie die neue Arbeitswelt in der Praxis aussieht. Der IT-Experte ist beim Sensorenhersteller verantwortlich für das Thema Industrie 4.0 und steht jetzt im Keller unter der Fabrikhalle. Hier sind die Heizungs- und Lüftungssysteme untergebracht. Bucher bleibt neben einem unscheinbaren Kästchen stehen: „Wenn diese Pumpe ausfällt, steht hier die Produktion zwei Tage lang still.“ Und dann zeigt Bucher auf Kabel, die aus der Pumpe ragen. „Sie führen zu Sensoren, die permanent die Schwingungen der Pumpe überprüfen.“ Sobald es zu Abweichungen kommt, schlägt der Fühler Alarm, sodass Mechaniker rechtzeitig eingreifen können, bevor es zum Totalausfall kommt.
Für ifm ist diese moderne Technik gleich doppelt bedeutsam: Erstens stellt die Firma ihre eigene Fertigung nach und nach um – und zweitens produziert sie selbst genau solche Sensoren, die für die Industrie 4.0 nötig sind: Strömungssensoren, die Wasser- und Luftbewegungen messen, gehören genauso zum Sortiment wie Füllstandssensoren, lasergesteuerte Abstandsmesser – und Tausende weitere Produkte. „Als wir auf die moderne Produktion umstellten, hatten manche Mitarbeiter natürlich auch Berührungsängste“, erinnert sich Oliver Bucher. Der IT-Fachmann programmierte kurzerhand eine Anwendung, mit der jeder die Vorteile selbst erleben konnte. Er stattete das Fahrradhäuschen vor den Toren des Werks mit einem Sensor aus und jedes Fahrrad mit einem kleinen Chip. Wer mit dem Fahrrad zur Arbeit fährt, wird automatisch erfasst – die fleißigsten Radler bekommen Preise. „Vom ersten Tag an“, sagt Bucher und schmunzelt, „gab es in den einzelnen Abteilungen Wetten darauf, wer wohl gewinnt.“ Täglich loggen sie sich in das Industrie-4.0-System ein, um den aktuellen Punktestand zu kontrollieren, und machen sich so ganz nebenbei mit der Software vertraut.
Im Hauptwerk von ifm in Tettnang gibt es auch noch eine Handvoll klassischer Arbeitsbereiche: In einer Fabrikhalle sitzen dicht nebeneinander Arbeiter, die in Handarbeit einzelne Drähte zusammenlöten. Auch hier wird derzeit Schritt für Schritt automatisiert. „Wir bauen die gesamte Produktion konsequent um“, sagt Bernd Hausler, der Produktionsleiter. Man brauche künftig weniger niedrig qualifizierte Mitarbeiter, aber dafür mehr Informatiker, Facharbeiter, Ingenieure – das sei der Trend. Viele Mitarbeiter werden deshalb für komplexere Aufgaben weitergebildet oder für den Umgang mit den neuen Maschinen geschult. „Für manche hat die Welt, die sie seit Jahrzehnten kannten, einen Riss bekommen“, räumt Hausler ein. Aber gekündigt habe ifm keinem einzigen Kollegen, und das werde auch so bleiben: „Wir schaffen dank der Automatisierung eine gewaltige Produktivitätssteigerung“, sagt Hausler. Die gleiche Zahl von Mitarbeitern, heißt das, stellt jetzt viel mehr her als früher – deshalb können auch alle an Bord bleiben.
Versuchslabor für moderne Arbeit
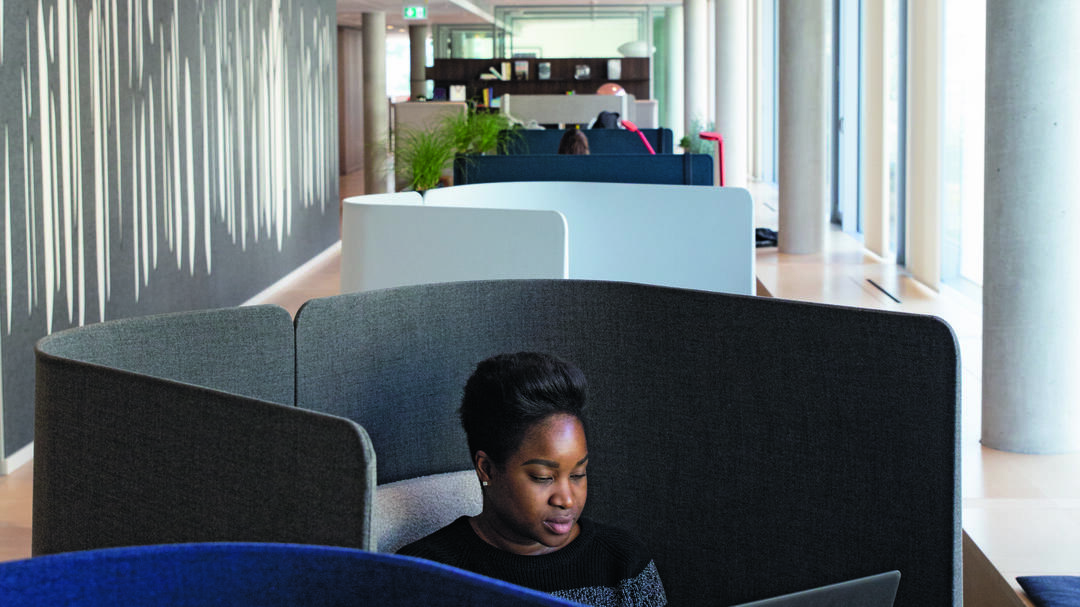
Wer vom Bodensee aus 200 Kilometer in Richtung Osten fährt, kann dort eine ganz andere Vision vom Arbeiten in der Zukunft besichtigen. „Wir sind hier die Versuchskaninchen für unsere eigenen Produkte“, sagt Helmut Kausler und lacht. Er arbeitet bei Steelcase, einem Büromöbelhersteller aus Amerika, der in bester Münchner Lage seine Zentrale für Europa, Nahost und Asien unterhält. Kausler steht im spektakulären Treppenhaus. Die Wände sind mit amerikanischem Nussbaumholz verkleidet, auf dem Boden liegen edles Parkett und langfloriger Teppichboden. Kausler und seine Kollegen haben hier den Trend in konkrete Formen gegossen, der durch die Büros in aller Welt schwappt: Es soll nicht mehr so formell zugehen bei der Arbeit. „Learning + Innovation Center“ nennt die Firma Steelcase ihr Münchner Büro, und tatsächlich wirken die fünf Stockwerke wie ein einziges Versuchslabor.
Eigentlich ist Kausler Lehrer, seit vielen Jahren aber berät er Schulen und Universitäten bei der Inneneinrichtung. „Vorher war hier der Sitz eines Energieversorgers, und der fünfte Stock gehörte ganz dem Vorstand“, erzählt Helmut Kausler. Jetzt habe man das Gebäude quasi umgedreht: Der Vorstand sitzt in offenen Büros im ersten Stock gleich über dem Foyer, der fünfte Stock mit seinem Panoramablick auf das Stadtzentrum bietet nun Schulungsräume und eine spektakuläre Dachterrasse für alle Mitarbeiter. Überall dazwischen sind Arbeitsplätze verteilt: Mal klassische Schreibtische mit großen Bildschirmen darauf, daneben gemütliche Sessel mit Fußschemeln und Klapptischen für den Laptop. Die Stehlampen sähen auch im heimischen Wohnzimmer gut aus. „Ich habe früher in Großraumbüros gearbeitet, mit Sichtschutzwänden zwischen den Schreibtischen. Und ich hatte auch schon einmal ein Eckbüro mit Vorzimmer, wo die Sekretärinnen im Prinzip nur dazu da waren, niemanden zu mir vorzulassen“, sagt Helmut Kausler. „Aber nirgendwo habe ich mich so wohlgefühlt wie hier.“ Natürlich muss er diese Sätze sagen, schließlich will er die Möbel verkaufen – aber im Kern geht es hier, auf den fünf Experimentier-Etagen, um etwas völlig anderes als den Vertrieb. Hier geht es ums Lernen.
„Wir gestalten Büros so, dass man etwas lernen kann. “
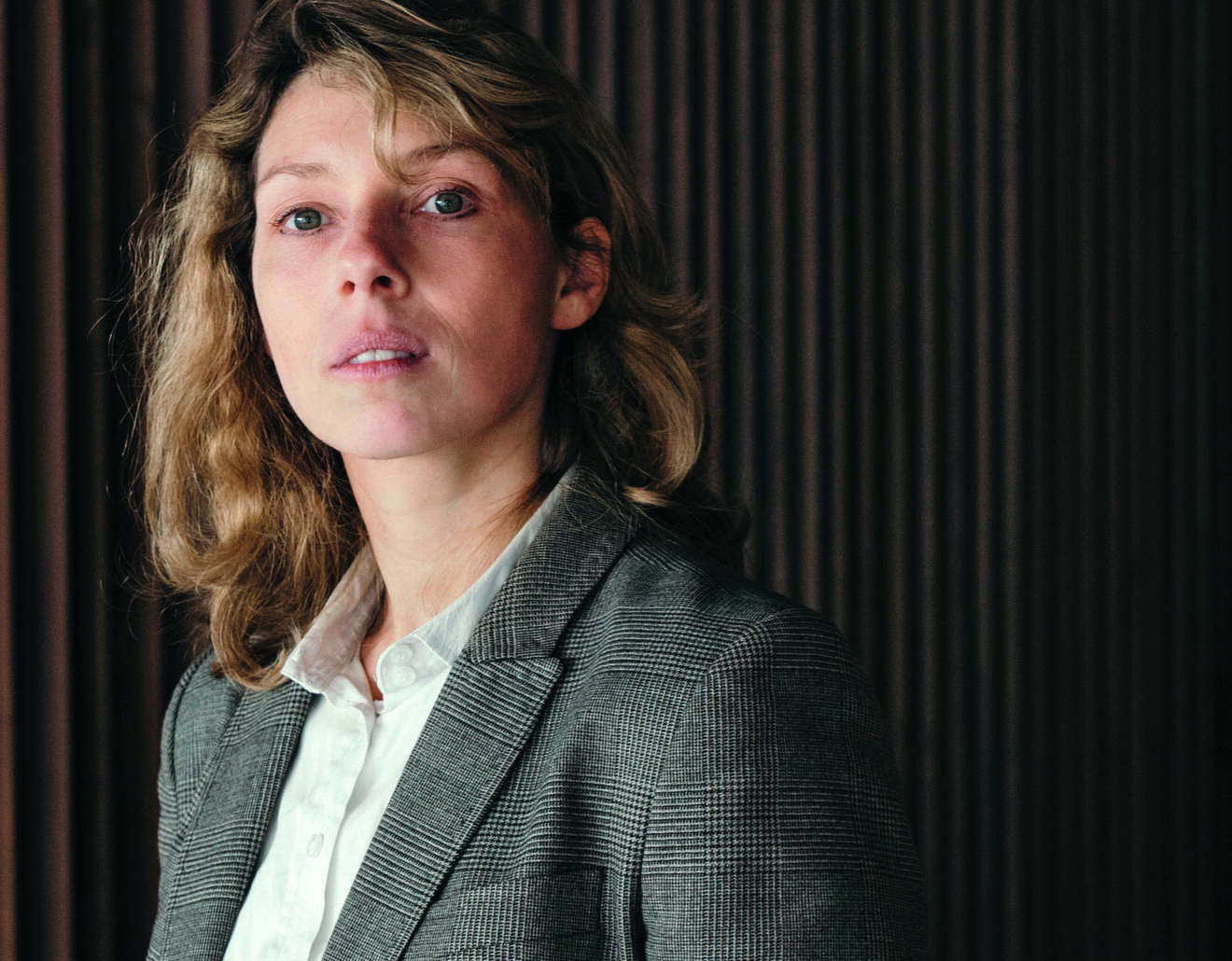
Die oberste Lernexpertin bei Steelcase heißt Nadine von Blücher. „Als ich mich hier einarbeitete, lag ein großer Schwerpunkt auf dem Netzwerken, dem Kennenlernen von Kollegen, der Entdeckung des großen Ganzen“, berichtet die promovierte Pädagogin. So ähnlich funktioniert die gesamte Weiterbildungsstrategie der Firma – die „70-20-10-Strategie“, wie sie Nadine von Blücher nennt: Lernen funktioniert zu 70 Prozent durch eigene Erfahrung, zu 20 Prozent durch Kontakte zu seinen Kollegen, etwa durch Feedback, Mentoring oder Coaching, und zu 10 Prozent in gezielten Schulungen. „Unser Gebäude ist ein einziger Gesprächsanlass“, sagt sie. Im Treppenhaus, an den Schreibtischen, in der Kantine, im Innenhof, auf der Dachterrasse – überall trifft sie ihre Kollegen, und oft entstehen nach zufällig gewechselten Worten neue Ideen. „In den 1990er-Jahren wurden in vielen Büros Kaffee-Ecken eingerichtet und die fest zugeordneten Schreibtische abgeschafft“, erzählt von Blücher. „Wir gehen darüber weit hinaus. Wir gestalten unsere Büros so, dass man auf Schritt und Tritt etwas lernen kann.“ Dazu gibt es drei Kategorien von Räumen , die den Bereichen „Denken“, „Tun“ und „Teilen“ zugeordnet sind. Je nachdem, an welcher Aufgabe ein bestimmter Mitarbeiter gerade sitzt, findet er die richtige Arbeitsumgebung.
Die Büros von Steelcase sind zugleich Arbeitsplätze der Mitarbeiter und Showroom für die Möbel der Firma – und bieten unzählige Anlässe, über Firmenkulturen nachzudenken. Pro Woche kommen Hunderte von Besuchern aus ganz Europa, um zu staunen und sich inspirieren zu lassen. Unternehmen schicken oft ganze Delegationen aus unterschiedlichen Abteilungen. „Wir drücken jedem einen kleinen Rechner in die Hand, auf dem er bei seiner Tour durchs Gebäude immer dann eine Taste drücken kann, wenn ihm ein Raum gut gefällt“, sagt Helmut Kausler. Bei der Auswertung dieser Daten komme es zu Überraschungen: Manchmal wollen die Mitarbeiter statt ihrer Einzelbüros lieber einen wohnlichen Großraum, manchmal wünschen sie sich Konferenzräume mit Tischen, die gruppenweise beieinander stehen. Wie die Mitarbeiter am besten arbeiten können, wie sie sich gern austauschen und wie sie am liebsten lernen würden – das kommt dabei schnell zutage. Die Erfahrung zeige, dass ansprechende Büros kein überflüssiger Luxus seien, sondern tatsächlich die Produktivität und die Kreativität erhöhen. „Wir haben unser Ziel erreicht“, sagt Helmut Kausler, „wenn Menschen nicht nur ihr Lieblingscafé haben, sondern auch ihr Lieblingsbüro.“
Dieser Beitrag erschien zuerst in: CARTA 2020 - Wieder mal moderne Zeiten
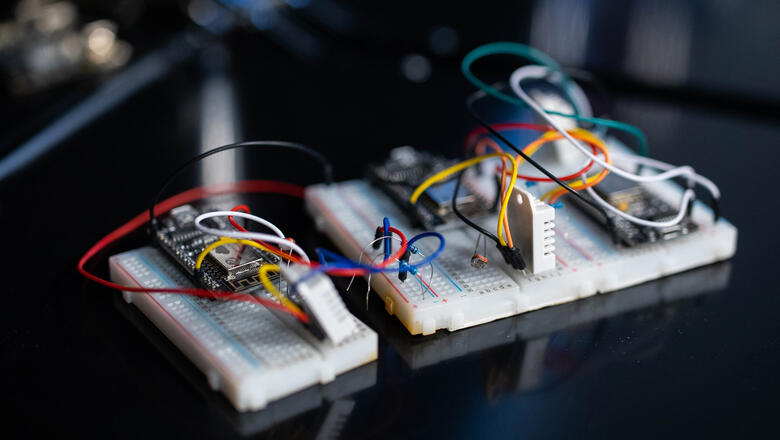